What is a passivhaus?
There are many advantages to building your own home, one of them is that you can choose your materials and systems to become more energy efficient.
This has many benefits, including:
- Reducing your energy costs
- Healthier more consistent internal environments
- A house that is better for the environment
Amid the hype, everybody seems to want to build a passive house which is known as passivhaus in most of Europe. However, it is worth taking a step back to understand what a passivhaus is and what building one involves.
What does the term passivhaus mean?
A passivhaus is a building that has met a performance-based energy standard, this term originates from Germany during the 1990s and is based on the energy efficient design and systems that reduce a buildings ecological footprint.
How is passivhaus standard achieved?
A passivhaus must achieve an optimum figure of airtightness which is set out in the passivhaus standard. Passivhaus homes must be ventilated using a mechanical system, which preheats ventilation air by recovering the heat from stale air as it leaves the building. This type of system is becoming more mainstream in the UK and particularly the norm for highly insulated buildings.
Most passive houses, use a mechanical ventilation heat recovery system (MVHR) during winter, as the buildings are designed to be extremely airtight, this prevents uncontrolled heat escaping through gaps and cracks. The MVHR system runs constantly even during the summer at a low level, by using a considered ducting design to keep noise low and create fresh air through constant air changes.
What are the key features of a passivhaus?
- High levels of insulation, around double that of a standard property
- High-performance triple-glazed windows, and insulated frames
- An airtight building fabric, around ten times more airtight than a home built to current UK building regulations
- A greater thermal bridge 'free' construction, through careful design and detailing of junctions
- A highly efficient mechanical ventilation heat recovery system (MVHR)
- Efficient and optimum design, incorporating energy efficient features and fittings
- Consideration of solar orientation
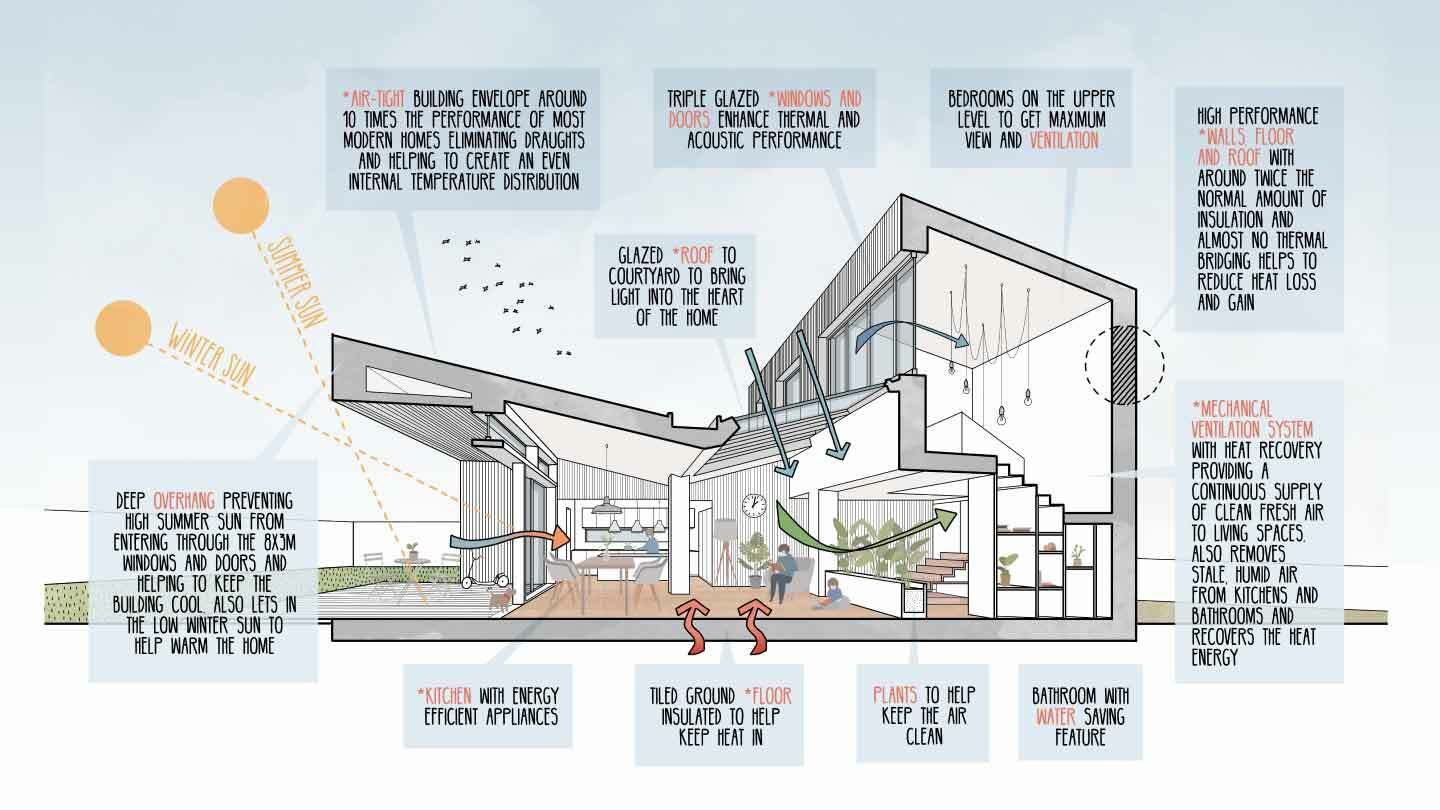
Passivhaus Construction
The construction of a passivhaus needs to be highly insulated and airtight, as more passivhaus projects are built, skill levels in the industry are starting to grow. However, there is a cost involved with the construction of a passivhaus, as it tends to need more care, attention to detail and high-quality build. This initial cost is expected to offset the savings in energy bills during the lifetime of the home, along with added comfort levels, which in itself holds an implied monetary value.
What are the benefits of building to passivhaus standard?
Due to the long payback duration, most people need reasons beyond energy efficiency before deciding to build a passivhaus.
Well, here are a few:
- Easy to live in and thermally comfortable, with no draughts and even temperature distribution
- Healthy environment with good indoor air quality provided by the mechanical ventilation system
- Good acoustic performance, provided by a combination of very well insulated walls, airtightness and triple-glazed windows
- Lower running costs due to energy efficiency
What is passivhaus design?
Most believe that a typical passivhaus is based on a simple box design, but this is not necessarily the case. However it is true to say that numerous junctions and intricate designs make it much harder to achieve the required standard. House sizes and footprints should be designed to the optimum, avoiding unnecessarily large homes and aiming to contain the most space, as efficiently as possible. Optimising the sun is an important element in the design of a passivhaus, for example, a plot may have beautiful views to the north, but wouldn’t be ideal for large viewing windows. Or, it may have a south facing garden, but the sun is blocked by trees or hedges, maximising south facing windows will help heat rooms during the winter.
With highly energy-efficient homes there is a danger of overheating in the summer, especially if there are large areas of unprotected glazing to the south and west. Effective design can overcome this by ensuring that these windows have appropriate shading, including but not limited to overhangs or shutters, this is a standard feature of southern European houses. Automated blinds can also be installed, these can be set to close if the internal temperature rises beyond a set point, to prevent overheating.
The use of natural light is also an important part of passivhaus design, as it helps reduce energy consumption, and the need for turning on artificial lights. This could be achieved through top-lit enclosed courtyards, roof lights and sun tunnels. Incorporating these elements into the design will help the house become more energy efficient.
Fittings and fixtures should also be carefully considered and sourced. We are all too familiar with energy rating certificates, and one should be choosing these with these ratings in mind.
As designers become more familiar with passivhaus standard, they will develop their skills to be more expansive with energy-creative designs. A good designer will start to take advantage of the benefits of different plots, client briefs and budgets with energy efficiency and comfort as important factors. This is especially important as building regulations move to more zero carbon buildings in order to gain approvals from local authorities .
Passivhaus myth-busting guide
How significant is passivhaus in delivering sustainable housing?
Passivhaus standard focuses almost entirely on the energy used by buildings and their internal comfort environments. It has successfully demonstrated that you can live comfortably in houses built in this method, in a variety of European countries and further afield. They are low in energy consumption with the opportunity to add additional renewable energy systems, as demand increases or where further funds become available. This means they can be a good option if you are looking for a more sustainable lifestyle.
Passivhaus standard has had a major influence on the direction of policy in many countries. Some even adopting the passivhaus standard as optional or mandatory in new construction. This is positive news, helping to drive the development of new products and skills within the industry.
Does building a passivhaus home, have to result in architectural design compromise?
Building to passivhaus standard does have some impact on design. In the same way all energy-efficiency standards, must meet a certain criteria. Simple volumes and shapes tend to work better than complex designs. With the construction materials needing to be carefully considered to performs efficiently. The size and orientation of windows are also important to manage solar gains as well as heat losses.
However, none of this means that designing to the passivhaus standard is difficult. Our Elsworth passivhaus demonstrates that an architecturally interesting design can still meet the standard, the challenge is to merge the design considerations with energy-efficiency.
Is it true that you cannot open the windows in a passivhaus?
This is a myth. The energy efficiency of the house in the coldest part of winter relies on closed windows, but that doesn’t mean you cannot open them if you wish.
The house will simply get cold, and it will take a while to warm up to the optimum temperature. A Passivhaus is designed to require very little heating, without the need for a standard heating system. In the long term, this helps save money, as there is no boiler or radiators to maintain or replace.
Can I add renewable energy systems?
Yes, you can. There should be plenty of roof space to accommodate solar thermal or photovoltaic (PV) systems. Solar thermal may offer great savings as it can provide over half your annual hot water.
Adding PV panels also helps to reduce national grid energy consumption. Grid energy is not “clean” energy, as we still use a lot of coal and gas in the UK. PV panels can help reduce the energy used in a passivhaus to nearly zero over a year, or in some cases it can generate a small income through 'feed-in tariffs'. But only if there are sufficient PV cells and the energy is well-managed.
Before deciding on whether or not to go for a passivhaus you need to decide whether certification is important to you or not. If it is, all aspects and performance levels will need to be met, using the PHPP package. This is the standard criteria to which a certified passive house designer will base their plans and outcomes, both at the design stage and once it is built.
If certification is not important, there is nothing stopping you from deciding what aspects of a passive house you would like to adopt, based on your needs, lifestyle and budget. Working with your designer you can carefully consider your options and incorporate these into your home from the outset.